Engineered Clay Barriers
Engineered Clay Barriers are designed based on the safety functions providing the necessary long-term containment and isolation and cost-effective engineering solutions.
Laboratory and clay barriers
All aspects required for the barrier design and production, and its regulatory approval are covered. The path starts from clay material acquisition chains, composition analyses and engineering parameters determination, goes through testing and modelling the performance of the barrier system and its components, and ends with predictive modelling verifying barrier evolution and performance for the thousands of years required. Collaboration with Repository Technology and Long-Term Safety allows requirements management for the safety functions, and cost-effective engineering solutions.
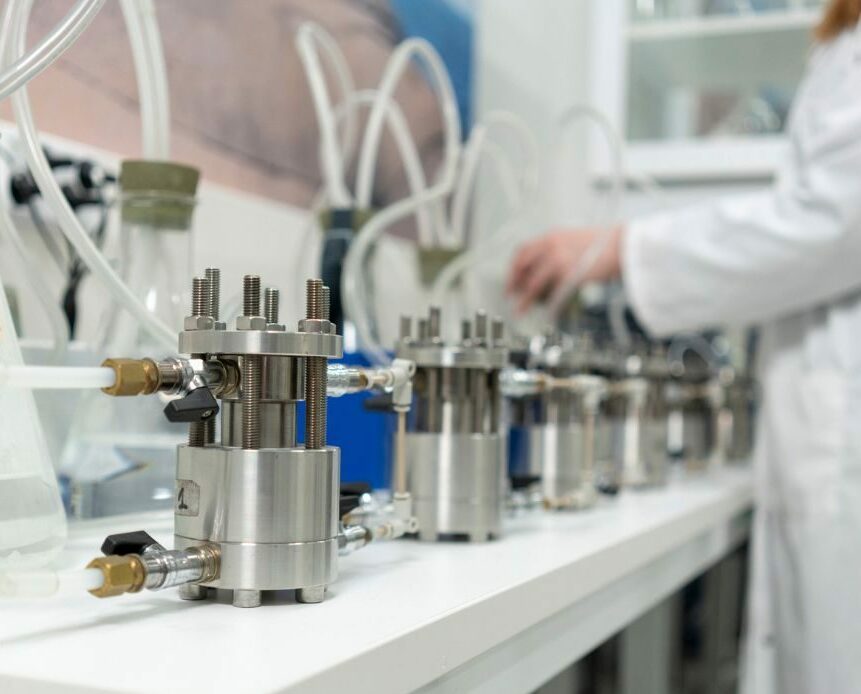
Laboratory for testing of clays and engineered clay barriers
Our laboratory is specialized in testing of clay material characteristics and performance of engineered clay barriers. Examples of our standard laboratory measurements on clays are:
- Cation exchange capacity (spectrophotometric, internal standard)
- Specific density (volumetric, internal standard)
- Swelling index (ASTM D 5890 – 11)
- Swelling pressure (constant volume, internal standard)
- Hydraulic conductivity (constant volume internal standard based on ASTM D 5084-03, or under load, internal standard)
- Suction (using psychrometer and/or hygrometer, internal standard)
- Water retention curve (internal standard)
- Uniaxial compression test (based on ASTM D 2166-06, internal standard)
- Tensile strength (beam test, internal standard)
- Consolidation (internal standard)
- Thermal conductivity (based on ASTM 5334-14, internal standard)
Our testing facilities provide opportunity to test performance of engineered clay barriers from millimetre up to several metres scale, and processes within a specific clay barrier or at the interfaces to other barriers such as wetting, swelling and sealing, erosion, freezing and thawing, chemical alteration, homogenization, and penetration of clay material into rock fractures. Examples of such performance testing include assessment of the effect of various factors such as flow rate or elevated temperature on clay barrier hydration, swelling, density distribution, mechanical properties or chemical properties. The tests are carried out in testing systems that are designed specifically on your needs.
Modelling
Mitta Engineering is an expert on modelling of
- thermo-hydro-mechanical (THM) processes occurring in clays and clay barriers, as well as host rock
- evolution of heat and liquid transport in backfill and other clay barriers and rock.
Most of the modelling references are from spent nuclear waste repositories but have been applied to other environments as well e.g. heat storages in rock cavities. Thermal coupling to geo-engineering is a strength of our modelling capability. Both analytical and numerical solutions are utilized. The numerical modelling code applied for modelling of THM processes in clay barriers is Code_Bright (FEM).